Keith Post, Bricking Solutions, talks us through his wealth of experience on matters of proper refractory installation.
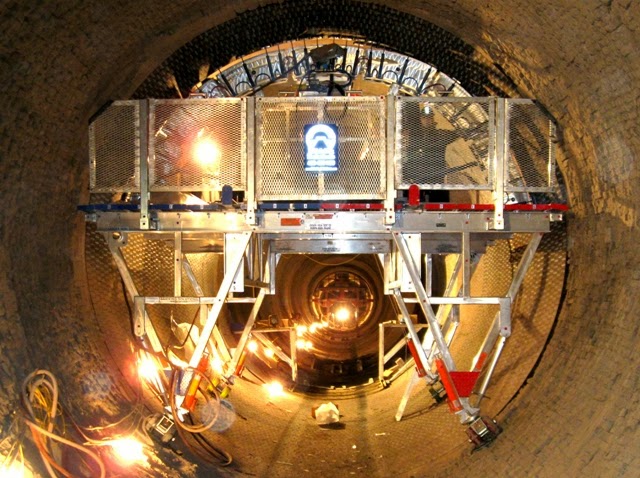
ximage24
The kiln is down again. These are five words guaranteed to make people cringe with thoughts of added expense to the yearly budget, lost production and safety concerns due to another unplanned outage. Questions are asked, and doubts surface about the type of brick being used and whether or not it was zoned properly. Having waited for the end of the kiln’s proper 24-hour cool down period and after it has been descaled, let’s say that, upon investigation, it becomes clear that a portion of the refractory is missing.
In fact, there are two or maybe three rows missing from the site of a shell deformation left by the failure of an earlier campaign. Now begins the tedious task of removing what is required, contacting a contractor, or having the appropriate plant personnel ready for installation. Once the brick is installed and the kiln fired, there is nothing to do but hope that nothing further will happen until the next scheduled downtime.
A meeting with a representative of the refractory company will be called prior to installation in order to determine the refractory type required. A proper analysis of brick samples will be conducted, but the timescales involved will invariably mean that the results will not be available until after the kiln is up and running. Determining whether to remain with the same type of refractory or choose a different one is discussed. The plant’s operating parameters have not changed, so what is different.
Case study
The company for which the author worked for 30 years was essentially set in its ways when it came to its choice of refractory contractors or installing plant personnel. This company formed a focus group, with the objectives of determining the best refractory types and their proper zoning, reducing refractory inventory to a basic amount, performing regulated refractory trials, determining the cause of any failures and offering technical assistance when and where it was required.
The most common cause of the failures observed within this organization was a lack of proper installation procedure. For the most part, workers did not have full knowledge of the procedures, and the result was that they were not able to develop a thorough understanding of the potential failures that could arise by not adhering to them. Once this issue was identified and full and proper instruction was provided on the installation processes, the rate of failures dropped significantly. The Focus Group would meet with refractory champions and production managers for a yearly seminar to discuss techniques, implement proper procedures, for kiln, cooler, cyclone and duct work alike. A strong emphasis was always placed on the inclusion of the actual mason or brick laborers that the given plants dealt with. This kind of supervision became evident from the minimized amount of downtime that the company experienced.
While it was clear that training was the key to more successful production runs, the Focus Group found that the implementation of this ideal was task within itself, especially when it came to contractors. Because a great deal of companies hire through union halls in North America, this was always a struggle. These methods don’t guarantee the same worker will come to each job, or even for consecutive days of the same job. Again, the time scales involved with a refractory installation simply do not allow for retraining of labor within the same project, and no amount of micromanagement could change that.
The next step
Time passed and the company disbanded the focus group, stating that there was “nothing left to achieve.” The results showed that this was somewhat shortsighted though, and failure rates began to creep upwards again. At the plants that the ex-focus group members had returned to, the group’s practices were still being implemented. Trials still used the same measures, and training was continuously being advanced and regulated, too. To enhance the goals and objectives that had been developed by the Focus Group, the author had contractors local to his plant perform a certification course for all employees working with the refractory group. The idea of the course was not the reinvention of the wheel, as it were, but simply to ensure that all workers entering the plant were aware of its minimum standards. These workers had to attend a course and pass with 75% minimum grade for working at the plant. All aspects of refractory installation for kilns, coolers, cyclones were covered and understood. Anyone that arrived at the plant not trained would not work as a mason; in such cases, these workers were offered work as a laborer.
Certification
An accepted certification process for the masons and workers meant vast improvements for the plant, which made premature failures rare. Production time, and therefore overall output, was increased, and unnecessary downtime was reduced. In short, all plant processes were augmented. For the masons and workers, it demonstrated serious goals to be achieved, and a better understanding of both administrator and customer requirements. These measures allowed a working relationship to progress into a partnership.
The course itself concentrates on all types and aspects of refractory installation, from kilns to cyclones, whether they require brick, castables, gunites, shotcrete or plastics. In many respects, it focuses on a principle of ‘sticking to the basics’, eliminating the shortcuts and guess work that have always been the Achilles heel of refractory installation. It seems like a simple thing, but the provision of the correct equipment can improve safety standards of all applications, and this is no different. Once put in place, the application of effective training, equipment and knowledge can equate directly to safety, quality and advancement.
Conclusion
As far as advancements in refractory go, it is the simple oversight of one very important requirement in the developmental stages that has the tendency to hold things back; it often seems to be the case that the installation worker is neglected as someone who is expected to follow instructions that have not been fully explained to them. Perhaps worse is that they are overlooked as a valuable resource – these workers have the kind of hands-on experience that could be tapped for opinions on how to make installation procedure as efficient as possible. The workers are the foundation of any refractory installation program, and utilizing their skills correctly can ensure the program’s success.
In summary, there are ways to prevent unexpected outages, which can be very time consuming and costly. If the masons and workers are not trained properly, there could be an even higher cost, with the potential for premature failures arising from a poorly executed installation. If there is no system or set of procedures in place to quickly rectify such situations, then unexpected costs can soar even higher. Having a well oiled system where refractory improvement and installations procedures are continually being researched, as well as having a good labor crew certified on specific plants procedures will ensure that no one is left having to hear those five words again.
Contact us here for more information.