Ever wish someone could fix your problems?
We can’t do much about a bad haircut or a leaky roof, but when it comes to refractory maintenance, we love a good challenge. Whether it’s an access, installation or safety challenge, we work with customers to design and build custom solutions.
Here are a few examples of special projects that required creative solutions.
Challenge: Rebricking a Torpedo Ladle
We have lots of experience manufacturing bricking machines for rotatory kilns. That has been the mainstay of our company for more than 50 years.
Then a customer inquired about a bricking rig for a torpedo ladle. This gave us the chance to re-imagine a product that has worked well in the cement industry and re-engineer it into a solution for the steel industry. From that request, the torpedo ladle bricking machine was born.
It includes many of the features customers like about our standard bricking machine, such as pin-together design for easy assembly. Some of the key differences include:
- Platform that extends the full length of the torpedo ladle
- Tapered ends to accommodate the shape of a torpedo ladle
- Cylinders that tilt individually to align brick with the taper
Through conversation with the customer, we added another standout feature: Two arches that allow a team to start bricking from each end and work toward the middle. Not only did the customer get a custom solution for their application, they were able to double their brick installation productivity.
Challenge: Assemble a Kiln Access Ramp in Limited Space
Like the bricking machine, we’ve manufactured kiln access ramps for years. Customers like them for several reasons:
- They are custom-designed for an ideal fit.
- They are constructed from strong but lightweight 6061-T6 aircraft aluminum with a 6,800-kilogram (15,000 pound) live-load capacity.
- They are rigorously tested for safety and can withstand 3 times the maximum load capacity.
- They are modular, allowing installers using a forklift to assemble them in as few as 1.5 to 2 hours.
One customer, however, needed a sizable ramp — 4 x 5.4 meters (13 x 17.75 feet) plus a nose that was 1.5 x 3.4 meters (4.83 x 11.17 feet) — but didn’t have the space on the burn floor to use a forklift truck for assembly. Instead, their team needed to be able to manually handle and assemble the components. As a result, each piece needed to be less than 75 kilograms (165 pounds).
Another challenge was that they wanted to use the same ramp for two kilns; however, one kiln was only accessible from the right and the other only from the left.
We were able to devise a solution and deliver exactly what they needed — a large ramp that was lightweight enough for their team to assemble by hand and could be configured two different ways to accommodate access for both kilns.
Challenge: Move Safely Through the Cooler
Another customer sought a safety solution — reassurance that personnel and equipment moving through the cooler were protected in the event any coating build-up unexpectedly loosened and fell.
Once again, we re-engineered an existing product. Our standard safety cages are designed to be on the move and carried by two people. This customer’s application called for a static solution. We custom-designed a 5.5-meter (18-foot) safety cage to mount on the bridge and provide protection for movement through that area.
Challenge Always Accepted
Do you have a refractory maintenance challenge? Let us know! Helping our customers come up with viable solutions is what we’re all about.
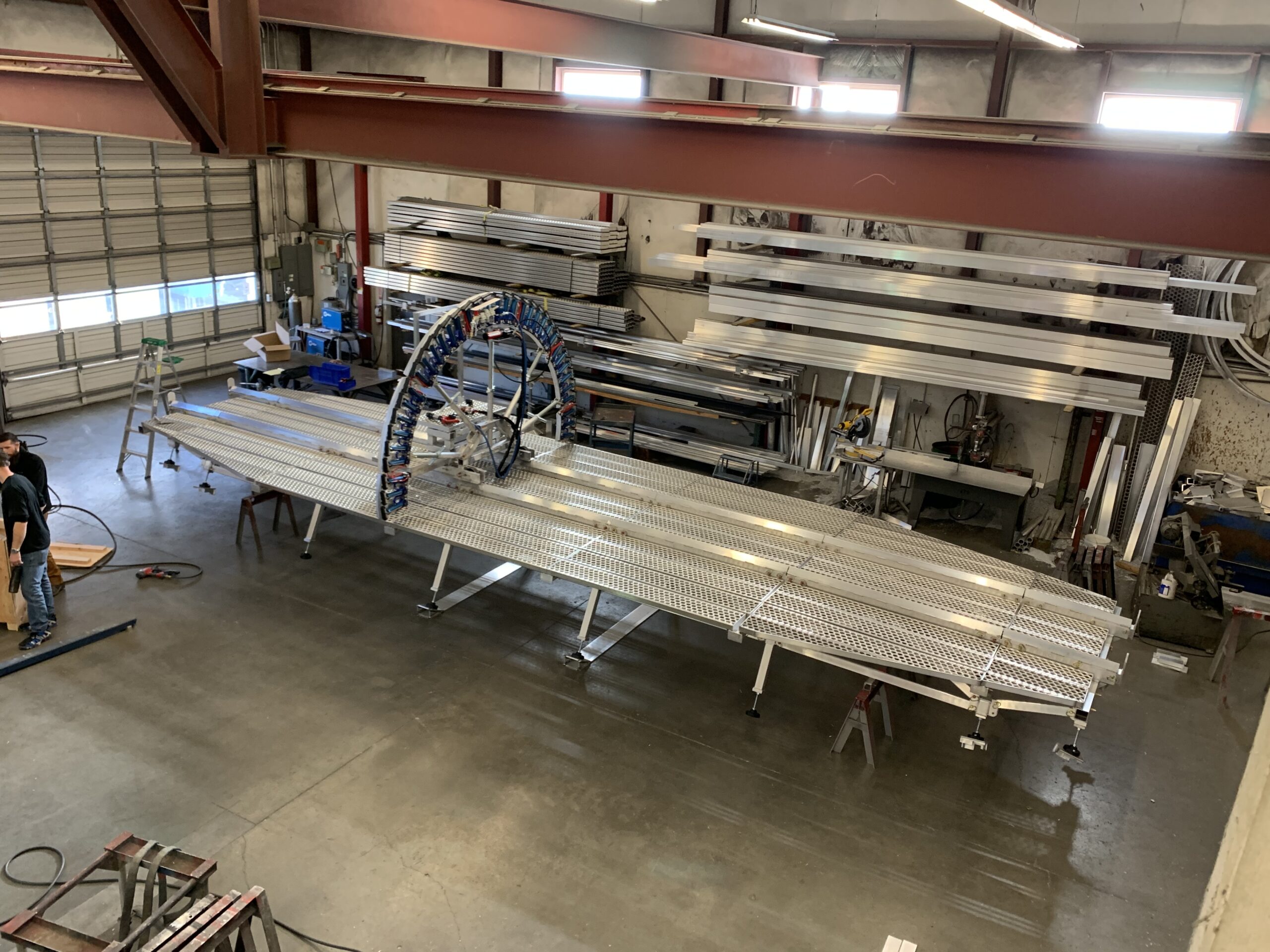
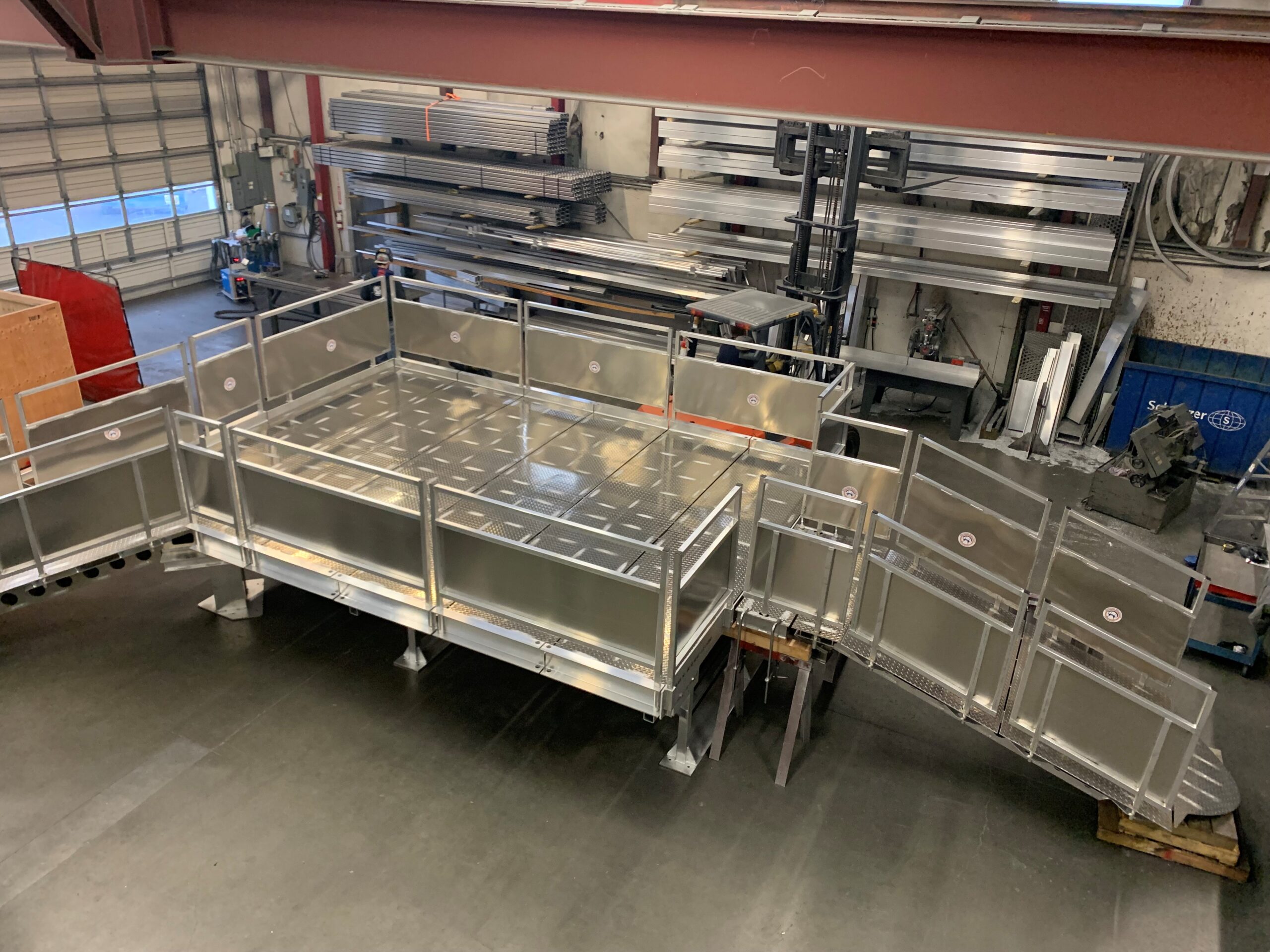
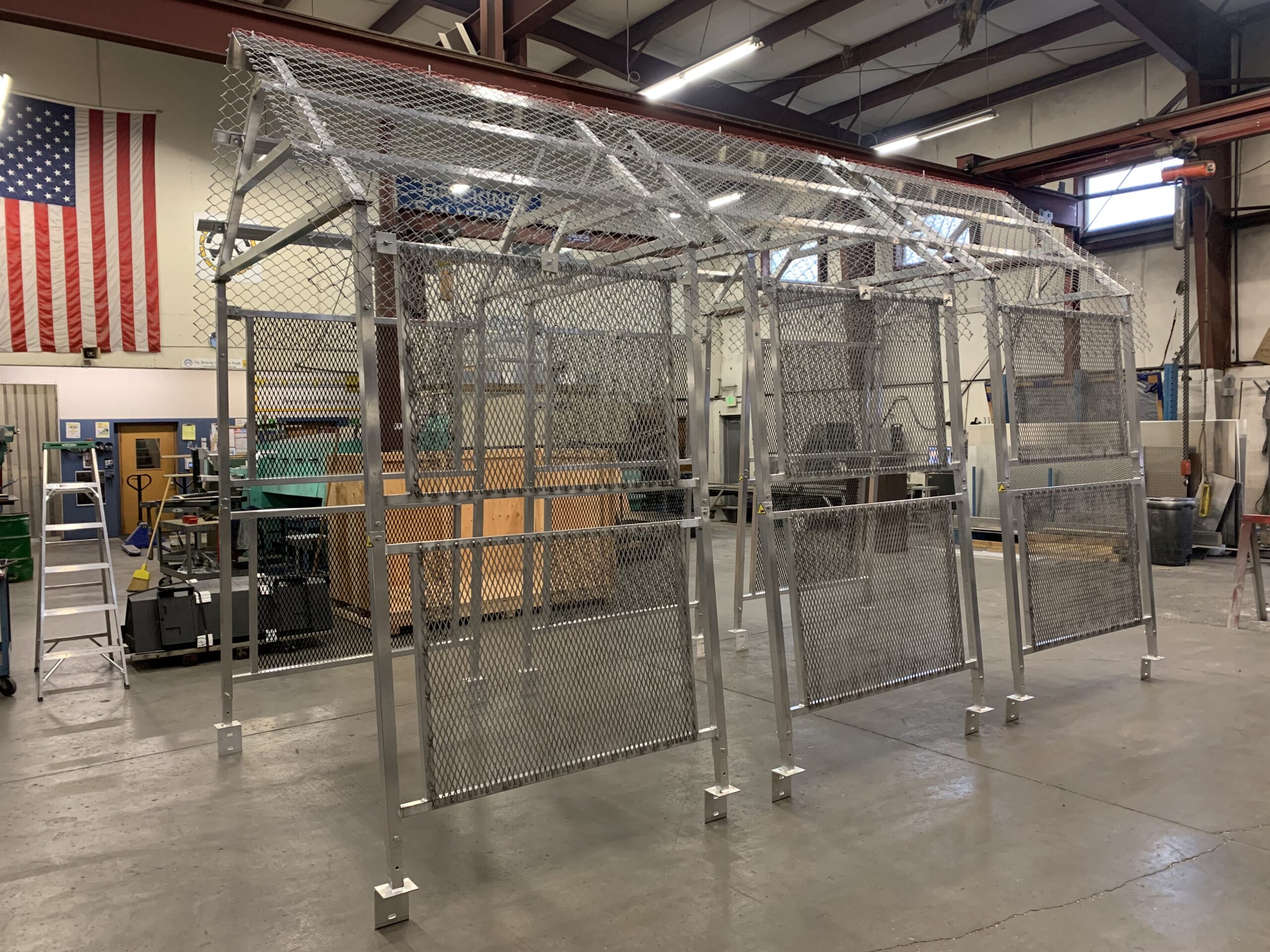